Industrial painting
What is industrial painting, and what are its uses?
Since industrial paint is more protective to aesthetic, it is commonly composed of coatings such as
- Epoxy
- Polyutherane
- Moisture cure urethane
- Fluoropolymer
These coatings contain long-chain polymer molecules. When these molecules bond with concrete and steel, reactive molecules like acids and alcohol lock to form a tough, flexible film.
Follow us
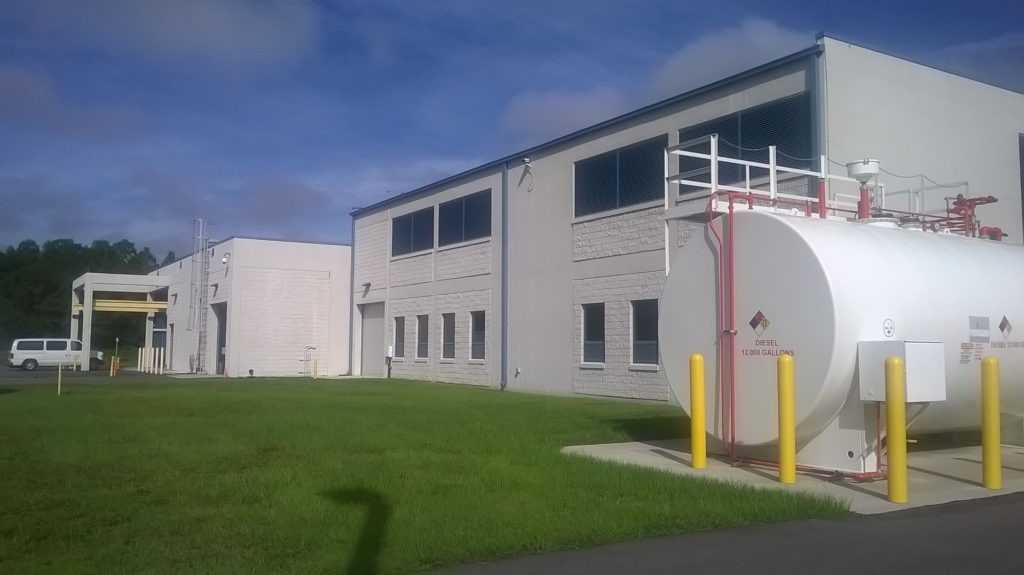
Materials
- All paints and consumables for a particular project shall be sourced from one manufacturer
only to have desired paint performance, guarantee and single point responsibility. The
containers are unbroken with their labels and tags intact. - Macventure mixes paints in factory supplied kit quantities, to assure the accurate correct ratio.
Mixing of partial kits is prohibited. Macventure only mixes the number of kits that will be applied well
within the pot-life time. - If the ambient temperature of the region in which the paints are being stored is below 4°C
the manufacturer’s data sheet is consulted for product-specific restrictions. - Additives, including thinner, color tints, and accelerators, are in exact accordance with the
paint manufacturer’s recommendations. Generic brand additives are not permitted. - Paints shall not be thinned beyond the ratios recommended by the manufacturer.
- Batch/test certificates are present.
- Macventure supplies Product Data Sheets (PDS) and Material Safety Data Sheets (MSDS) for all
materials used in the painting process. - The use of hazardous solvents is minimized. The control and disposal of these substances
comply with all national, regional, and local regulations. - Remaining Shelf life is at least 90% of the total duration at the inspection above.
- The Macventure project manager monitors and inspects the surface preparation, storage, handling,
mixing and application on substrate of the painting/coating and to ensure the compliance of
the specifications. - All paint equipment, including mixers, will be thoroughly cleaned before mixing of new
materials. - All paints and painting materials shall be stored only in rooms to be arranged by Macventure and
approved by the project manager for the purpose. All necessary precautions shall be taken to
prevent fire.
Surfaces Preparation
- Surfaces and cavities which could be damaged or contaminated by the surface preparation
and/or painting will be masked or plugged appropriately. This includes openings in vessels
and piping, and many of the items which are not to be painted. - All oils, greases, tars, salts, and similar materials or contamination will be removed per SSPC
SP 1. This includes the use of high-pressure washing with industrial detergents, followed by
rinsing with clean water. - Prior to paint application all surfaces will be assessed and treated in accordance with ISO
8504:2000. - All loose rust and loose mill scale will be removed. All weld splatter and slag, shall be chipped
or ground off. All sharp edges, points, burrs, weld platters, weld peaks, roughness, and raised
surface defects will be removed by power sanding or grinding (and intact shop primer where
applicable) to St3 ISO 8501-1:2007 / SSPC- SP3 / Pt3 of JSRA SPSS-1975. - All edges of the existing coating will be sanded to taper the thickness and thereby make for a
smooth transition with the new paint. - The surface will be lightly abraded with a bristle blaster and GSE ensures it will be free of
dust and dirt prior to application of coatings. - The ground shall be covered.
- If the surface preparation reveals a defect in the material of any structural or pressurecontaining
component, such as cracks, pitting or weld porosity, the client shall be promptly
contacted. No coatings shall be applied until the client has explicitly accepted the defect or
its repair. - Once achieved, the specified surface preparation standards must be maintained until all
areas are prime painted.
Application of paint
- All coating materials shall be mixed and thoroughly stirred in accordance with the
instructions of the paint Manufacturer. Sufficient agitation to maintain good mixing shall be
applied until the product is used. If air is entrapped in the product during mixing/stirring,
sufficient time should be allowed for the air bubbles to escape before application. - To the maximum extent practicable, each coat of material shall be applied as a continuous
film uniform thickness free of porous. Any spots or areas missed in application will be
recoated and permitted to dry before the next coat is applied. Applied paint must have the
desired wet film thickness. - For coating different color shades are used for primer and intermediate coats, for ease in
monitoring and identification of the number of coats - Each paint coat will be smooth, free of defects, fully bonded, and of proper thickness. Any
runs and sags will be removed. The top coat shall have a smooth and uniform color and
finish. - Instruments, machined or polished bright metal surfaces, the mating surfaces of flanged
joints, and the insides of open pipe ends shall be protected during surface preparation and
painting. - Macventure will supply and lay drop cloths to protect other work, equipment, and surfaces. After
completion Macventure cleans off any spilled or spattered paint. - No coat shall be applied until the preceding coat has dried and cured as recommended by
Paint Manufacturer. Next coat will be applied within the time stipulated by the paint
manufacturer. - Before over coating, over-runs, drips and smears shall be removed and any coating damage
or imperfection will be repaired. The material shall be considered dry for re-coating when
another coat can be applied without the development of any film irregularities such as lifting
or loss of adhesion of undercoats. - Before overcoating an epoxy paint, the surface shall be checked for amine blush. If any
greasy or waxy film is detectable, then the entire surface shall be thoroughly washed with
clean water and dried. - Contamination of the surfaces between coats shall be prevented. If contamination does
occur, surfaces shall be pressure washed and dried before the next coat of paint is applied. - No paint shall be force dried.
- No drier shall be added to paint on the job unless specifically called for in the manufacturer’s
specification for the paint. Paint shall be protected from rain, condensation and
contamination until dry. - To minimize the risk of damage, no lifting, transportation, erection or fabrication operations
shall be done before the paint has been fully dried and/or cured. - Damaged areas, defects in the coating system such as over-runs, drips and smears that have
to be removed or areas with inadequate dry film coating thickness shall be re-cleaned. - Only thinners specified by the paint Manufacturer will be used.
- The temperature of the paint shall be per the product data sheet.
- After the item is finish painted, it shall be marked to identify the paints that were used by
manufacturer and product number, and the date. The markings are be made directly on the
equipment on permanent labels. - Application restrictions, we cannot paint:
o During fog, mist or rain.
o When the relative humidity is 85 percent or above.
o When the surface temperature and/or ambient temperature is below 10°C.
o When the surface temperature and/or ambient temperature is above 35°C.
o When the steel surface temperature is less than 3°C above the dew point.